What is a plain slideway?
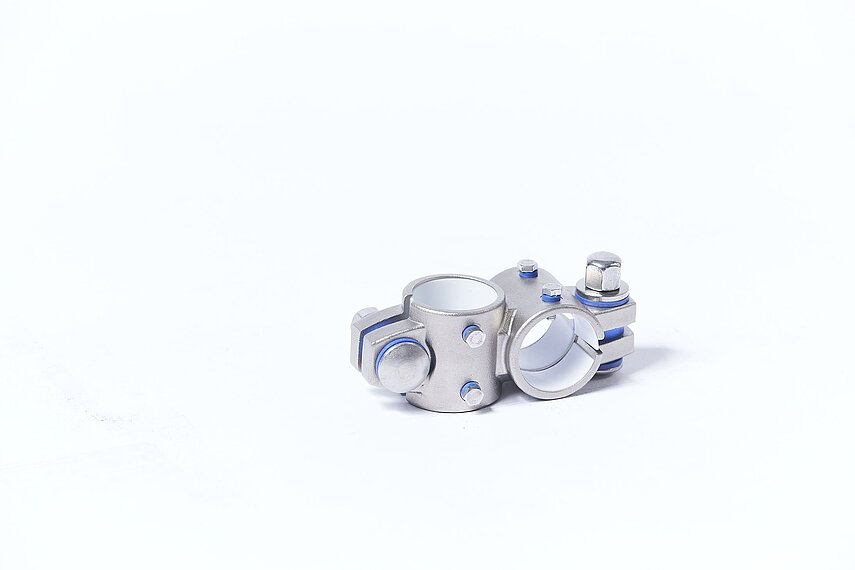
Plain slideways are linear guides free of backlash. The moved elements are not supported by balls or rollers; rather, they slide over form-fitting connecting elements. These connecting elements consist of linear unit connectors or sliding blocks and a rail guide. The sliding blocks wrap around the rail so that movement is only possible in one direction.
Plain slideways come in the following types:
- Hydrodynamic
- Hydrostatic
- Aerostatic
- Magnetic
Hydrodynamic slideways travel over a lubricant film which is maintained by means of an interior cavity.
On a hydrostatic slideway, the lubricant film is maintained by an external pump.
Aerostatic slideways make use of an air cushion. They do not require any additional lubricant and move very smoothly.
Magnetic slideways operate with a permanent or electrically activated magnetic field. They combine low friction with excellent controllability.
Advantages of plain slideways
Plain slideways offer the following advantages:
- Simple design with few parts
- Reliable positioning and precise movement
- Low-noise, damped operation
- Lubricant-free designs are possible
- Resistant to external influences, even in designs utilizing lubricants as long as special measures are taken
- Self-braking properties
Guide systems utilizing slideways are simpler in design and offer more reliable positioning than roller-based guides. They have significantly fewer parts than linear guides based on rolling bearings. This reduces wear and also makes them less expensive. The form-fitting sliding elements or blocks prevent any movement other than the desired direction. Aerostatic and magnetic slideways require no lubricant and are practically silent. They are suitable for dry running. Appropriate add-ons, such as bellows, can make lubricated or unlubricated slideways resistant to external influences such as sand or dust. The damping properties of the plastic elements on the sliding blocks and rails make the slideway immune to vibrations and impacts.
If the electric or pneumatic energy supply fails, the slideway stops automatically. Plain slideways are not subject to overrunning as is experienced with roller guides.
- Increased startup resistance
- Low efficiency due to increased friction
- Higher forces required for generating movement
- Some lateral freedom of movement due to oversized guide elements
- Less stiffness compared with rolling bearing guides
In the resting state, the full surface of the sliding blocks rests on the slide rails. This results in the described startup resistance. Not only must this resistance be overcome, the force required to do so must also be absorbed. This situation is particularly severe with pneumatic drives, for example. Systems in which precise positioning is critical should therefore ideally be driven by a spindle guide since these possess self-damping properties.
Overall, these advantages and disadvantages make slideways without rolling bearing support best suited for positioning parts in loading and unloading processes. They are an excellent choice for pick-and-place systems that have low requirements with regard to positioning tolerances. Thanks to their greater stiffness, roller-guided linear motion offers an advantage in high-precision applications, such as CNC machining, 3D coordinate measurement, or the precise movement of very heavy components.
Contact
Do you have special challenges in the area of research and development? Contact us. We look forward to your inquiry and will help you find just the right solution for your application.